Selecting EDM Machines: Voltage, Dielectric Fluid, Machine Structure, and Axis Options
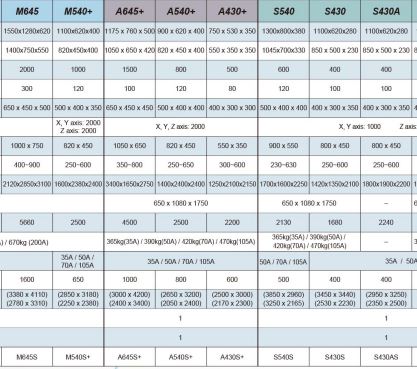
When selecting an EDM machine, understanding its key influencing factors and various applications is crucial. This article will delve into voltage settings, dielectric fluid selection, machine structure differences, and the number of synchronized axes, helping you choose the most suitable EDM equipment.
1. Voltage Settings in EDM
Voltage is a critical variable in EDM, with high and low voltages each having their own advantages and disadvantages. Typically, two parallel and additive discharge circuits are designed: one for ignition with a small current discharge circuit (ignition voltage) and another for processing with a large current discharge circuit (processing voltage).
- Sinker EDM: The precision of the corners is crucial, usually using a low voltage (80V~100V) as the processing voltage, supplemented by a high voltage (120V~330V) as the ignition voltage to enhance processing efficiency. In the processing of sinker EDM, it is essential to minimize electrode wear to achieve high-precision corners. Low voltage helps reduce electrode wear but decreases processing efficiency, hence the need for high voltage to assist ignition and improve overall efficiency.
- Wire EDM: Focuses on cutting speed and material removal rate, typically using a high voltage (220V) as the processing voltage, and a low voltage (80V~120V) as the ignition voltage to reduce the discharge gap and increase thermal efficiency. The design goal of wire EDM machines is to maximize material removal rate while maintaining cutting precision. High voltage helps in rapid material cutting, while low voltage ignition helps control the discharge gap, making the heat more effective in melting the workpiece.
- Small Hole EDM: Similar to wire EDM, it focuses on drilling speed, usually only concerning penetration speed while ignoring surface roughness, thus having fewer voltage and current steps or lower resolution.
2. Dielectric Fluid Selection: Deionized Water vs. EDM Oil
Dielectric fluid plays a crucial role in EDM, affecting processing efficiency, precision, and the surface quality of the workpiece. Common dielectric fluids include deionized water and EDM oil, each with its unique advantages and applications.
-
Deionized Water:
- Advantages: Fast processing speed. Due to its relatively high conductivity, it enables faster material removal, suitable for high-efficiency applications.
- Disadvantages: Workpieces tend to oxidize post-processing, with larger discharge gaps and poorer corner precision. It can also lead to oxidation on the workpiece surface.
- Applications: Generally used in wire EDM machines.
-
EDM Oil:
- Advantages: Smaller discharge gaps, better corner precision, and workpieces are less prone to oxidation.
- Disadvantages: Slower processing speed. Due to its lower conductivity, processing speed is relatively slower, suitable for applications requiring high precision and surface quality.
- Applications: Generally used in sinker EDM machines, such as German Oelheld EDM oil. Sodick has also introduced wire EDM machines using EDM oil to enhance processing precision. These machines focus on processing precision and the final surface quality of the workpiece, hence choosing EDM oil as the dielectric fluid.
3. Differences in Machine Structure
The design of an EDM machine's structure directly affects its processing precision and stability. Different structures are suitable for different processing needs and applications.
-
C-Type Structure:
- Advantages: The processing spindle is fixed, providing the highest rigidity. Since the spindle does not move, the entire machine's rigidity is very high, suitable for processing small molds.
- Disadvantages: Since the processing tank needs to move, the weight of the workpiece and the processing fluid in the tank can affect the X/Y axis movement precision, suitable for small workpieces.
-
Head-Type Structure:
- Advantages: The moving axis is above the electrode, allowing for greater workpiece load capacity than the C-type structure. This design can carry heavier workpieces, suitable for large workpiece processing.
- Disadvantages: When the Y-axis moves to the negative limit, the Z-axis may drop due to a shift in the center of gravity, typically sacrificing some travel to enhance precision.
-
Moving Column Structure:
- Advantages: The moving axis is above the electrode, overcoming the center of gravity shift problem in the head-type structure, providing a more stable processing environment.
- Disadvantages: Occupies more space. Due to structural requirements, these machines usually take up more space.
-
Gantry Structure:
- Advantages: Composed of two moving column structures, it can carry heavier electrodes. This design can handle larger and heavier electrodes.
- Disadvantages: High cost, large footprint. Due to its complex structure, manufacturing costs are higher, and it occupies a larger area, suitable for large mold processing.
4. Number of Synchronized Axes in Sinker EDM
The number of synchronized axes in an EDM machine directly affects its processing capability and flexibility. Different numbers of axes are suitable for different complexities of processing needs.
- Traditional Sinker EDM: Single-axis machines cannot expand holes, and the side surface roughness cannot be finely finished, suitable for simple processing needs.
- General CNC EDM: Three-axis processing can meet most processing needs, providing basic flexibility and processing capability.
- Four-Axis EDM: Adds spiral machining and transfer printing functions, with a C-axis that allows automatic angle adjustment for further processing.
- Five-Axis and Above EDM: Mainly used for path machining combined with targeted hole expansion processing, offering the highest flexibility and precision, suitable for the most complex and fine processing tasks.
Conclusion
Choosing the right EDM equipment requires consideration of various factors, including voltage settings, dielectric fluid selection, machine structure design, and the number of synchronized axes. Understanding these key influencing factors will help you make more informed decisions and select the most suitable EDM machine to meet different processing needs.
We hope this article provides valuable information and helps you make the best decisions in the selection process of EDM equipment. If you have any further questions or need more advice, please feel free to contact us. We are dedicated to providing you with the most professional support and services, helping you achieve success in the field of EDM.