- Home
- Products
- Die Sinking EDM
- CNC EDM A SERIES
CNC EDM A SERIES
Advanced technology EDM
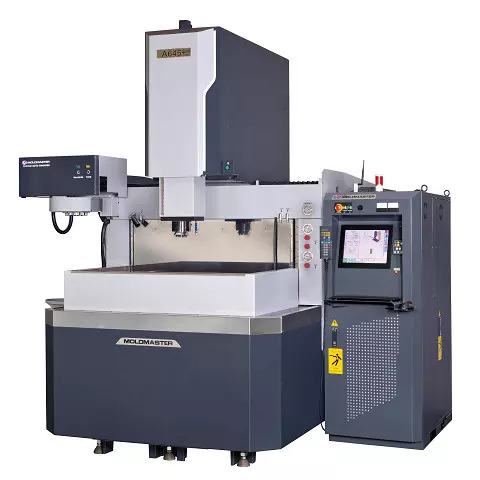
Feature
MOLDMASTER A-series with high precise & elevating work tank& full automatic technology will support mold production to be high-speed and manufacturing with no personnel. (Taiwan Patent NO:M373250 )
[Elevating work tank]
Accessible space design and programmable height control of the work tank; Enable closer machine operations from three different directions and easily to in and out workpiece by robot.
[Newly Designed High Precision Head for Z Axis]
Features heavy weight and strong rigidity main axis implementation, which keeps traverse rate at 8 m/min high-speed and also ensure the main axis usage durability from daily operation.
[Increased machine accuracy](With Optional ±0.1C Cooler Equipped, Under Constant Temperature)
The fully-covered body machine design makes the machine dust free in the structure, and the cooling oil system keeps the machine temperature as stable as possible. The X, Y, Z axis are calibrated with laser equipment to achieve ±1µm during axis traveling.
[Newly Designed Power Supply & Control System]
With the new power supply and control system which extends the life of electrical boards, reduces the electrode wear. The fuzzy control technology enables high traverse rate at 8 m/min without over shoot.
[Power -Less Than 0.05% Super-Low Wear Circuit]
The advanced digitized power technology control the production of every electrical current and adopt equal energy's discharge circuit design to make after-finework polishing very easy. Now, electrode wear ratio referring to SL circuit below 0.05% from thick to thin only need a electrode to complete high precision work. Cleaner machining in corners, rising points, channels, ribs, and sharp angles contribute to a very low electrode wear. Specially providing 2mm ~ 5mm small piece and small clearance discharge conditions will be most suitable for Electron Information Precision Mold Industry to work with particular low wear. A modern Fuzzy intelligent control system provides the auto adjustments of machining parameters and improve the machining efficiency and safety. More easy to use, a beginner can operate like an expert.
[Automatic Back Flushing Equipment](optional)
Reduce secondary discharge to improve machining performance and precision mold corner, cost down and replacement filter time.
[HQSP The High Quality Super Polishing Equipment](optional)(Taiwan invention patent: I229622)
HQSP is able to substantially increase luster Surface Area Limitation to approximately 400cm². The time for completion of luster surface area is approximately 1/2-1/5 longer, to reduce the machining surface cracking and saves time and efforts in manual polishing operations after machining.
[Windows interface](optional)
- More user friendly graphical interface improves the user familiarity with the system also reduces the time of learning.
- Diversification measurement function (3 points for Center, unsymmetrical groove unsymmetrical column, parallel calibration)
- Multi-workpiece automatic measurement with the same size, the coordinates can be recorded for the convenience of program editing.
- Programmable measurement, the measurement function can be edited into program, for the needs of automation operation.
- Program check, alert the user program errors and the cause.
- Remote monitoring by mobile phones, pads, or laptops anytime anywhere.
- Remote program editing on laptops anywhere.
- Compatible with EROWA calibration equipments.
- Compatible with any coordinate measuring machine(CMM) electrode compensation files.