News & Events
The Advantages of EDM Machines: Comparing the Disadvantages of CNC Machines
July 09,2024
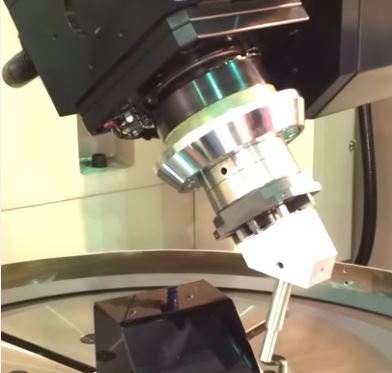
The Advantages of EDM Machines: Comparing the Disadvantages of CNC Machines
CNC machines are essential equipment in modern manufacturing. As CNC machines' processing capabilities become increasingly strong, the market for EDM (Electrical Discharge Machining) machines has shrunk. However, in certain aspects, EDM machines have clear advantages over CNC machines. This article will delve into the advantages of EDM machines and explain why some markets must choose EDM machines over CNC machines.
Precision Tolerances
EDM machines are renowned for their superior precision tolerances. They operate using non-contact machining, allowing for extremely high precision parts as long as room temperature and fluid temperature are properly controlled. Therefore, EDM is often used as the final process in mold and parts manufacturing.
Wide Range of Applications
EDM machines have a wide range of applications. They can process various hard-to-cut materials, such as hard alloys, high-strength steel, titanium alloys, and honeycomb structures. These materials are often difficult to handle with traditional machining, but EDM can easily manage them. Additionally, without the limitation of a high-speed rotating spindle tool, EDM machines excel in processing complex geometries and micro parts. This makes EDM machines indispensable tools in specific industries like aerospace, medical equipment, and microelectronics.
Cost-effective Consumables
Compared to CNC machines, EDM machines are more economical in terms of consumables. The electrode materials used in EDM, typically graphite or copper, are relatively inexpensive, easy to obtain, and reusable. On the other hand, the tool materials required for CNC machines, such as hard alloys and high-speed steel, are not only expensive but also wear out quickly during machining, requiring frequent replacement. Furthermore, EDM machines consume fewer consumables, only requiring timely replacement or replenishment of filters and machining oil, which further reduces production costs.
Low Machine Failure Rate
EDM machines have a relatively low failure rate due to their machining principles. EDM removes material through electrical discharge, a process that causes minimal wear on mechanical components. Consequently, the maintenance and upkeep costs are lower. In contrast, CNC machines, operating under high-speed cutting and heavy loads, tend to experience more wear and tear on mechanical components, leading to higher repair and downtime costs. This gives EDM machines a significant advantage in maintaining stable production lines.
Manufacturer Optimization and Innovation
Manufacturers of EDM machines continuously strive to optimize the processes and performance of their equipment to enhance market competitiveness. By introducing advanced control systems and automation technology, modern EDM machines have made significant strides in precision, efficiency, and ease of operation. For example, advanced EDM machines can achieve six-axis simultaneous machining, automatic electrode changing, integration with full factory automation systems, CAD/CAM to NC programming, and machine thermal deformation compensation, greatly improving production efficiency and machining quality. These innovations have led to the increasing popularity of EDM machines across various industries.
Conclusion
In summary, EDM machines demonstrate significant advantages in precision tolerances, wide applications, consumable costs, machine failure rates, and market positioning. These advantages make EDM machines indispensable in many industries. At the same time, manufacturers of EDM machines continue to innovate, optimizing their processes and performance, further solidifying their irreplaceable market position. Choosing EDM machines not only enhances machining quality and efficiency but also reduces production costs, achieving higher economic benefits. Therefore, for applications requiring high precision and complexity, EDM machines are undoubtedly a better choice than CNC machines.
CNC machines are essential equipment in modern manufacturing. As CNC machines' processing capabilities become increasingly strong, the market for EDM (Electrical Discharge Machining) machines has shrunk. However, in certain aspects, EDM machines have clear advantages over CNC machines. This article will delve into the advantages of EDM machines and explain why some markets must choose EDM machines over CNC machines.
Precision Tolerances
EDM machines are renowned for their superior precision tolerances. They operate using non-contact machining, allowing for extremely high precision parts as long as room temperature and fluid temperature are properly controlled. Therefore, EDM is often used as the final process in mold and parts manufacturing.
Wide Range of Applications
EDM machines have a wide range of applications. They can process various hard-to-cut materials, such as hard alloys, high-strength steel, titanium alloys, and honeycomb structures. These materials are often difficult to handle with traditional machining, but EDM can easily manage them. Additionally, without the limitation of a high-speed rotating spindle tool, EDM machines excel in processing complex geometries and micro parts. This makes EDM machines indispensable tools in specific industries like aerospace, medical equipment, and microelectronics.
Cost-effective Consumables
Compared to CNC machines, EDM machines are more economical in terms of consumables. The electrode materials used in EDM, typically graphite or copper, are relatively inexpensive, easy to obtain, and reusable. On the other hand, the tool materials required for CNC machines, such as hard alloys and high-speed steel, are not only expensive but also wear out quickly during machining, requiring frequent replacement. Furthermore, EDM machines consume fewer consumables, only requiring timely replacement or replenishment of filters and machining oil, which further reduces production costs.
Low Machine Failure Rate
EDM machines have a relatively low failure rate due to their machining principles. EDM removes material through electrical discharge, a process that causes minimal wear on mechanical components. Consequently, the maintenance and upkeep costs are lower. In contrast, CNC machines, operating under high-speed cutting and heavy loads, tend to experience more wear and tear on mechanical components, leading to higher repair and downtime costs. This gives EDM machines a significant advantage in maintaining stable production lines.
Manufacturer Optimization and Innovation
Manufacturers of EDM machines continuously strive to optimize the processes and performance of their equipment to enhance market competitiveness. By introducing advanced control systems and automation technology, modern EDM machines have made significant strides in precision, efficiency, and ease of operation. For example, advanced EDM machines can achieve six-axis simultaneous machining, automatic electrode changing, integration with full factory automation systems, CAD/CAM to NC programming, and machine thermal deformation compensation, greatly improving production efficiency and machining quality. These innovations have led to the increasing popularity of EDM machines across various industries.
Conclusion
In summary, EDM machines demonstrate significant advantages in precision tolerances, wide applications, consumable costs, machine failure rates, and market positioning. These advantages make EDM machines indispensable in many industries. At the same time, manufacturers of EDM machines continue to innovate, optimizing their processes and performance, further solidifying their irreplaceable market position. Choosing EDM machines not only enhances machining quality and efficiency but also reduces production costs, achieving higher economic benefits. Therefore, for applications requiring high precision and complexity, EDM machines are undoubtedly a better choice than CNC machines.